DIY Self-Driving - Part 3. Wiring Harnesses
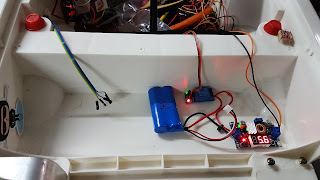
Please Note: Unlike most of my projects which are fully complete before they are published, this project is as much a build diary as anything else. Whilst I am attempting to clearly document the processes, this is not a step-by-step guide, and later articles may well contradict earlier instructions. If you decide you want to duplicate my build, please read through all the relevant articles before you start. In the previous post we looked at getting a motor driver up and running, and I realised I breezed over the process of how it was all connected. This article will (hopefully) address that shortcoming. Because this is a mobile project, vibration and the like will take a toll on connections and as we know, poor connections will lead to poor results. For this reason, I am going to take you through my process of making up wiring harnesses to suit our car. Clearly unless you are using the same car and modules as me your wiring is going to vary, but...